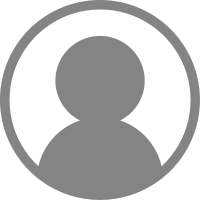
Menu
All materials of construction have individual characteristics which call for special consideration in design, fabrication and installation. Aluminium is no exception and needs to be installed in proper fashion if best use is to be made of it and maximum service is to be obtained.
Most of the standard aluminium alloys supplied for architectural and structural applications (e.g. McKechnie Aluminium 6060, 6063, 6106 and 6005a, 6061 etc.) perform very satisfactorily in normal exposed positions. The immunity of aluminium to the atmosphere arises from the protective nature of the oxide film which acts as a barrier to corrosion. For many purposes, decorative as well as protective, the naturally-formed oxide film is thickened by anodising and the protective value of the oxide film is thus considerably increased. The comments which follow apply mostly to unanodised aluminium.
In every climate where the atmosphere is at all humid, building and engineering materials undergo some chemical change with the passage of time and are subject to some form of corrosion.
Specific Modes of Attack
Several characteristic modes of attack on aluminium may be distinguished. In the presence of specific substances simple chemical attack may occur. Attack of aluminium by very weak corrosive solutions, such as contaminated rain water, is often insignificant if not prolonged, but it becomes important if circumstances cause the solution to be retained in contact with the metal. Sodden timber lying flat on aluminium, or moist insulation in contact with it are examples of absorbent material acting with a poultice effect. The corrosive solution is held continually in contact with the metal and rapid attack may result.
Crevice effect describes the acceleration of attack when moisture is lodged, for example, in the crevices of riveted or bolted joints in a structure, or when moisture is held by surface tension between the aluminium surface and some object lying against it.
It is possible for a building material when wet to liberate some specific chemical which can corrode aluminium used in the structure. This is corrosion by moisture exudation. Those which may attack aluminium are chiefly from alkaline building materials such as freshly-set plaster, mortars and cements and also acids from certain timbers when wet or unseasoned.
Corrosion of aluminium may be accelerated through contact with another metal in moist or wet conditions and this is known as galvanic corrosion. The two metals, together with water present, constitute a cell, causing a small electric current to flow and leading to corrosion of the less noble metal.
For example, when copper or steel is in contact with aluminium under above conditions aluminium will corrode but when zinc (galvanised surface) is in contact with aluminium then zinc will corrode.
Stainless steel and aluminium form an exception because the combined resistance of the two protective films impedes the current flow, thus reducing galvanic action.
General Means of Preventing Corrosion
The methods of preventing the corrosive effects just described really amount to the avoidance of the conditions which lead to them. Often it is impossible to avoid all the conditions but at least one form of preventive action can be taken and this will be adequate.
As moisture or liquid is essential to corrosion, the exclusion of moisture prevents its occurrence, but the choice of method depends on the nature of the problem. Poultice effect may be tackled by a moisture-proof barrier applied to the aluminium surface. Crevice effect is eliminated if the crevices are filled or stopped. Sometimes the trouble can be countered by designing a component to eliminate moisture traps, or making all contacting components of aluminium and eliminating particular contaminating constituents in, say, water which enters the crevice.
Mastics and putties (linseed oil) are satisfactory in contact with aluminium. Putties give good adhesion to aluminium where sound installation practice is followed, for example, by allowing the metal surface to weather, thus forming a key or, alternatively, by applying an etch primer. The choice of thermal insulating materials for use with aluminium must allow for condensation when the system cools below the dew point. This is because some insulation's contain chloride or alkali which can be leached out and may give rise to corrosion.
For detailed information dealing with the effects of specific materials and chemicals on aluminium the McKechnie Aluminium's Technical Services Department will be pleased to offer advice. There are many forms of assembly where water may be trapped in pockets because of exposure to the weather or condensation. There are several ways in which an accumulation of water may be prevented. For example, drainage holes may be drilled or complete drainage may be assisted by avoiding completely horizontal surfaces. When designing it is important to bear in mind, however, that surface tension tends to keep small holes filled with water until it evaporates. The size of the holes is therefore important.
When joining aluminium by bolts or studs to other metals it may be possible to use non-absorbent inserts of plastic, rubber or neoprene. Corrosion may be prevented sometimes by adding inhibitors to oppose the reaction of the active corroding agent. Zinc chromate contained in priming paints for aluminium acts as an inhibitor.
Aluminium in Contact With Other Materials
A number of specific materials commonly encountered in building construction are now considered for their corrosion influence on aluminium. These fall into three main categories, iron and steel, non-ferrous metals and non-metals.
(a) Iron and Steel
In contact with structural steel aluminium suffers attack when a good electrolyte is present, such as sea water or condensed moisture in industrial areas. Several treatments can be applied. to the steel such as metal spraying, galvanising, zinc or cadmium plating, painting with zinc-rich paints and so forth.
(b) Non-Ferrous Metals
Reference has already been made to the main non-ferrous metals likely to be encountered in building construction where contact can exist with aluminium. Contact with copper and its alloys must be avoided and chromium or cadmium plating, for example, is a satisfactory means to prevent this.
Frequently corrosion between aluminium and other metals can be avoided by lacquering, painting or sealing joints so that moisture is excluded.
(c) Non-Metals
Aluminium alloys used for building purposes have good corrosion resistance to concretes, mortars, plasters or fibre cement products. However, when freshly mixed some of these materials release traces of alkaline products which may be sufficient to stain aluminium. Splashing of these products onto aluminium, while not sufficiently corrosive to affect strength, does produce an unsightly, stained appearance. Contact with stone or brickwork, particularly when more open-grained and wet, can have a similar effect. Some separation by spacers at the joints should be effected. In very many applications, particularly indoor, contact between aluminium and timber has been successfully used. However, some more strongly acid timbers in damp environment can cause corrosion.
Plastics are virtually without action on aluminium in most conditions of service. Rubber is also without action on aluminium. Adhesives are available for bonding aluminium. Suitable adhesives should not contain in excess of 0.1% chlorides (e.g. NaCl).