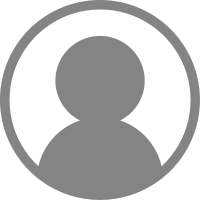
Menu
McKechnie has a proud history of extrusion in New Zealand, dating back to 1947 when we began with our brass extrusion mill. Today, as pioneers in aluminium extrusion in New Zealand, McKechnie continues to embrace the latest technological and manufacturing advances.
Explore McKechnie's history and discover our key milestones.
New Zealand manufacturers approached the McKechnie UK Board with a proposal to establish a brass extrusion mill in NZ.
McKechnie Brothers (NZ) Ltd incorporated on 27th February 1951.
Five-acre site on Carrington Road within New Plymouth City boundary purchased and site development commenced.
Key staff from United Kingdom led by W Hayes, (subsequent chairman of directors of New Zealand Company), arrive in New Zealand 6th April 1952.
First NZ employee engaged – Ron England 25th July 1952.
Stages in the assembly of the Shaw Extrusion Press (No.1) up to January 1953.
First brass log is cast 17th June 1953.
Shaw Press (No.1) extrudes first brass billet into (1.25” Round Alloy W - C17700) 8th August 1953. An extensive shipping strike in New Zealand waters during 1952 hampered & delayed plant installation.
Section No. 100 extruded in November 1954.
Number of employees reaches 60.
Rufflette brass curtain track production commences.
Lombard Press (No.2) delivered 21st July 1958 following building extensions in September 1958.
Commencement of aluminium extrusion on Lombard Press (No. 2) from imported Kaizer billet. The first extrusion occurred at 3.32pm 18th December 1958.
Employee count reaches 130 by February.
Additional five acres acquired for planned expansion in New Plymouth.
First newsletter published in March.
Rufflette track production reaches 7,000 miles (11,265 km).
Shaw press (No. 1) achieves 300 billets in 24 hours on 23rd May.
Lombard press (No. 2) extrudes 5 tons of aluminium in 24 hours.
Purchase of fifty-eight acres of industrial land at Bell Block July 1961. Original works located within boundaries of the city of New Plymouth were considered too restrictive.
Rufflette track production reaches around-the-equator distance in January.
Carrington Road factory fire July 23, 1962. The fire started in the die-hardening shop, exploded into the roof and spread rapidly into the storeroom.
Development of Bell Block site begins in July.
Vice-Regal visit from Governor-General Sir Bernard Fergusson.
New Lombard press (No. 3) for aluminium installed at Bell Block.
Plant from Carrington Road transferred to the Bell Block site.
Official opening of the Bell Block factory by Prime Minister Rt. Hon. K J Holyoake on 3rd March.
Copper tube trials commence in July.
Three tonne – 600 kW Birlec furnace for brass melting commissioned.
Brass Ingot Foundry Building, Ball Mill & Rotary Furnace installed.
Copper foundry and No. 1 copper mill construction starts.
Loewy-Robertson 2,000-ton piercing Press (No. 4) installed & commissioned.
No. 5 Bay building for Aluminium Extrusion added (2,450m2).
Lombard (No. 2) Press moved from Brass Mill to No. 5 Bay, converted to Aluminium & new extrusion handling system added.
Lombard (No. 2) Press moved from Brass Mill to No. 5 Bay, converted to Aluminium & new extrusion handling system added.
Staff versus Works annual Rugby match at McKechnie’s football ground at the southeastern area of the site adjacent to Okey Road.
No 1 Copper Mill building extension (3,350 m2) and Copper Tube Manufacturing plant installed.
Copper Tube manufacture commenced November.
Copper Tube manufacture commenced November.
Extension to Administration Block.
ARL 29000 Spectro for metals analysis installed.
Standards Association of NZ granted McKechnie Metal Products a licence to use the Standard Certification Mark for its copper tube to NZS.1755.
Copper Foundry building extension erected.
“Sklenar” copper melting furnace and 3 strand vertical log casting machine installed.
No. 1 Copper Mill extended and (No. 2) 33,000lb drawbench installed.
Original anodising plant commissioned in November 1972. Established as “McKechnie Anodising Services Ltd” – and operated as a 50/50 venture between McKechnie and Christchurch Electroplating Company Ltd.
McKechnie Brothers (NZ) Ltd listed as a Public Company in NZ. Shares issued to NZ public.
No. 1 Drawbench (33,000lb) lengthened 400hp SCR drive and improved handling system added.
Personnel Block was erected next to main site entrance.
Clubroom built adjacent to café.
“Coreco” Swarf Drying Building and rotary furnace installed.
North west wing added to administration building
Fabrication Shop erected and plant installed.
McKechnie Metal Report - August 1977:
NZ Parliament Beehive Mural 1975 - current
No. 2 Copper Mill built and plant commissioned. Officially opened by Prime Minister Rt. Hon R D Muldoon. [15th September 1978]
Shaw Press (No. 1) damaged beyond repair and removed from site.
Lombard Press (No. 2) moved back to Brass Mill to replace the Shaw Press. Converted to brass extrusion, and coil handling equipment added.
“UBE” Press (No. 5 - 1800 US Ton) and gas fired tunnel furnace commissioned for aluminium extrusion (Nov. 1978).
“Precision Cutting” enhancements installed within Fabrication Department.
New company “Alspec aluminium Services Pty Ltd” was formed in Melbourne, Australia to distribute Aluminium products.
Toolroom building erected.
New “Agie” wire cut machines installed.
Wire Mill major expansion of capacity. Showa triple drawing block & Takashima wire strengtheners installed.
Anodising plant expansion.
ARL 34000 Spectro for metals analysis installed to replace ARL 29000.
Construction of Auckland Office and Distribution facility.
New Aluminium foundry equipment installed including a new melting furnace, heating furnace & Wagstaff 20-mould casting machine.
Lombard press (No. 2) upgraded for brass coil production.
Purchase of Jamec Tools Pty Ltd, J D Morris and Pem Tool Company Pty Ltd.
Anodising warehouse extension.
New Aluminium Ager installed.
Lombard Press (No. 3) major upgrade including addition of puller, Granco billet heater, PLC/Automatic control, improved container guiding & pump controls.
New Anodising Building and Plant commissioned.
New gas fired homogenising furnace installed and electric furnace transferred to Brass Mill to replace the Effco Brass Wire Annealing furnace.
Purchase of Admax Trading Pty Ltd, an Australian distributor of non-ferrous metals.
“McKechnie Pacific Limited” name change – 1st June 1988.
Alco Ladder production commissioned.
Automated Lombard Press (No. 3) together with associated improvements.
Major upgrade to Lombard Press (No. 3), adding belt conveyors and a new saw.
Re-established Wellington sales office in December.
900kW induction melting furnace installed in the aluminium foundry.
A 4,000 m² extension, Bay #6, completed in 1995.
Sutton Aluminium Press (1830 US TON, No. 6) commissioned in March 1995.
Tardis 1062 Dross Press installed to recover aluminium from dross.
McKechnie Metals Pacific Pty Ltd operations sold.
Kelly Control System installed on Press 6, optimizing extrusion.
Automation of Copper Tube Manufacturing (Twinsaw & Texas installation).
Aluminium packing upgraded and automated.
2MW Induction melting furnace (C Pot) installed in copper foundry.
Dangerous goods shed installed.
No 2 Copper Mill walls partially sound proofed.
Reciprocating compressors replaced with quieter screw compressors.
Methven Tap makers of Dunedin combined with HMC of Auckland.
Press 4 slack-water tank relocated to outside foundry building.
No. 1 Drawbench PLC installed.
Upgrade of power supply to D Pot Furnace and Loewy Press (No. 4) pumps.
Loewy Press (No. 4) main ram replaced.
US Filters Brass wire pickling effluent treatment commissioned.
Mesh stretching operation commissioned.
Anodising effluent control partially upgraded.
Equipment storage barn decommissioned.
Methven Tap makers of Auckland sold.
Nickel removal process for anodising effluent installed & extensive R&D commenced by KiwiTech.
Cantilevered hydraulic loader installed for C Pot copper melting furnace.
Canopy at copper foundry installed for unloading containerized charge material.
Site storm water control measures implemented for Brass & Copper foundries.
Pine forests removed to enable commencement of landscaping projects.
US Filters Brass wire pickling effluent treatment plant automated.
Copper Division sold to MM Kembla NZ Ltd.
Mesh stretching operation sold & relocated in Australia.
Brass division sold to Consolidated Extruders Ltd.
Pyrolysis furnace installed in Powder coat mill.
Smart Aluminium, Regency Aluminium, Accord Industries & Jamec Pen sold.
Distribution network throughout Australia sold for Brass, Copper & Aluminium.
Rail siding at Bell Block closed.
Native bush planted near rail siding.
Brass Wire production Mill removed from site.
Brass Rod production Mills removed from site.
Extrusion Press 2 removed from site.
Brass foundry & Coreco swarf drying plant removed from site.
Brass wire effluent treatment mill (IX Plant) converted for nickel extraction.
CNC router installed & upgraded in Fabrication.
Fabrication welding bay relocated to old brass wire.
Bulk acid & caustic storage upgraded.
Site roads concreted for heavy metal runoff control
CNC machining centre installed in fabrication.
New remelt furnace installed. McKechnie is the only aluminium extruder in Australasia to have an onsite remelt facility.
New Powdercoat plant commissioned on the main site
Windows and Doors venture commissioned.
Mazda / Ford bumper bar fabrication
McKechnie acquired OMEGA® Windows + Doors from Larry Hoyle (who founded OMEGA® in 1978). Since then, McKechnie has invested in the people and products to make OMEGA® suites the most innovative, modern, and effective products, recognised across New Zealand and internationally.
McKechnie becomes the first Aluminium Extruder in the world to gain third-party Enviromark Diamond certification and CEMARS product certification (now known as Toitū Enviromark Diamond and Toitū carbonreduce product certification). Learn more about our Toitū certifications.
Installation of the new "Giulia" extrusion press begins.
First aluminium billet is produced on the new press.
Final performance handover of the "Giulia" press from Italian supplier Turla. McKechnie is home to New Zealand's largest and most technologically advanced aluminium extrusion press, increasing plant capacity by 30-40%.
In January 2020, during our summer shutdown, a fire devastated a portion of our factory, but our team's resilience shone through as we worked tirelessly to rebuild and maintain customer orders. We emerged stronger than ever, committed to delivering the same quality and service.
Second powder-coating line installed and commissioned to increase our powder coating capabilities.
Whiting Holdings New Zealand advises acquisition of McKechnie Aluminium. Transaction completed end of July 2022. Ultimate Holding Company – Amari Australasia Holdings Inc.